How it All Began
As I mentioned in my last post for this build, I was in a rush for my previous season. My time was spent fighting understeer issues, improving the reliability of the chassis, and navigating financial dilemmas. With that being said, I didn't have aero as I knew it would cost money and take up time. Instead, I focused on affordable suspension improvements.
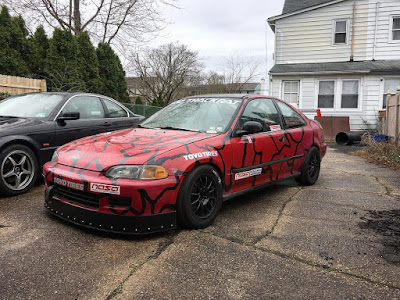
This Article Discusses Installing Budget, DIY Aero for Your Racecar
Using my used eBay pyrometer and some strings, I was able to dial in my alignment based on tire temperatures.
Soon-to-be Spec E30 Driver TJ and Alex Helping me With Tire Temps
Speaking with my friend Spencer I was able to experiment with used race springs on eBay to adjust spring rates. Spencer also turned me onto the sway bar setup I needed and my friend Alex, the owner of #TrashTeg, turned me onto deals to save me money on the sway bar setup.
Cheap, 800 lb/in, No-Name, eBay Springs
The NASA Northeast Competition School Director, Brian, is also a Honda Challenge driver, and through him I was able to determine which bushings were the most important to upgrade from rubber to spherical, rather than replacing all of them. Of course, Chris at Kingpin sold me the product I needed on closeout when he was trying to move product and this saved me money as well.
Best Bearings in the Business
During the off-season, I had a long list of upgrades and reliability and driveability improvements I needed to make to the car. One of them was to add a front splitter and a rear wing.
Rear Downforce
Honda Challenge H4 cars are not that fast. The speeds are on-par with Spec E30 and Spec Miata which both use stock-spec engines and share the same suspension setups for the most part. As a result, I knew that I didn't want a lot of drag.
People put rear wings on these FWD Hondas because it stabilizes the car in traffic (starts/restarts especially) and under braking-- two areas which are critical to laying down some fast laps and beating your competition. The rear wings also serve to stabilize the car in high-speed corners where suspension setup is less important than in low-speed, tight corners.
Carlos Valenzuela Driving a NASA SoCal Honda Challenge H4 CRX with Aero
The rear wing needs to be balanced with a front splitter, but we'll get to that at a later point in this post.
The best wing for my car would fit the following criteria:
A.) It's cheap
B.) It's small
C.) It works
D.) It's cheap
With that being said, i turned to my most trusted source for parts that work and are cheap: eBay.
eBay is full of cheap aluminum wings that are both light and functional. They may not be custom-made for your car, designed using CAD/CAM software, made of fancy carbon fiber, or have baller hardware, but for my purpose they would be perfect.
An eBay Wing Can be Had for Relatively Cheap
When I made it known that I was considering one, my friend, also a Honda Challenge Racer, Zephyr messaged me and told me he had an eBay wing from his old CRX race car that he would give me for free.
Zephyr's Old Race Car
The wing was perfectly sized for H4 as it's big enough to stabilize the car, but not big enough that it would considerably slow me down in the straights. So, I mocked it up to get an idea of where it would sit.
There were several factors I had to consider when fitting the wing.
Honda Challenge H4 rules state that the wing must be within the outline of the car's body when viewed from above, for one.
Secondly, wings generate more downforce when placed further aft of the chassis where they have better access to clean air. This second factor was something I gleaned from leisurely reading about race car aerodynamics. I'm sure there are exceptions to this assumption.
A Civic with a Legal Honda Challenge H4 Wing
I used a tape measure along the sides of the trunk, a chalk marker to mark where I wanted the centerline of the wing to be, some blue painters tape to ensure I didn't have a crooked reference line for mounting the wing, and a plumb bob to ensure my wing was within the legal limits stated above.
Using Chalk Marker to Make a Reference Line for a Non-Crooked Wing
When measuring to see if the wing is within legal limits, you must use a plumb bob. If you don't have a plumb bob, tie a nut to some kite string from the Dollar Tree. And use that. The point isn't to be fancy, it's to be fast.
A Picture From YouTube
Gravity is more accurate than the human eye. The pictures below illustrate this. It seems as though the wing is sitting just at the edge of the chassis. In reality, the wing is moved further forward than this by a considerable amount to ensure legality.
Viewing the Wing From Above
Next, I went to Home Depot and got the cheapest hardware I could find to attach the wing to the trunk. With each wing stand having six holes each, I knew I needed 6 x 2 = 12 bolts, 6 x 2 = 12 nuts, and washers for each nut/bolt on the outside and inside of the trunk (24 washers).
This was $20.
Home Depot Sends E-Receipts if You Provide Your Email-- a Very Useful Way to Track Build Costs
With the wing mocked up in its appropriate spot, I marked where I needed to drill and began putting holes in my crusty, 1993 Honda Civic trunk.
Wing Stands With Galvanized Bolts and Washers Inserted
Then, I opened the trunk and cut away the reinforcement structure in the areas where the bolts protruded. This would allow the bolts to sit properly (not crooked) in their holes and it would also allow access to someone with a wrench.
Inside of the Trunk
In the picture above, you'll notice that there are black plates underneath of the nuts and washers. These black plates are made of steel and are intended to reinforce the wing to ensure it meets objective "C."
These black, steel plates are made from spare oil pans I had laying around my garage. These oil pans do not sell for much used on eBay and the steel is too good to waste. If you have a vise with an anvil head and a sledge hammer you can easily straighten the metal out where it was stamped by the OEM to make a straight piece of sheet metal. I did something similar when mounting my MSD ignition.
Next, I knew I needed to set the angle of attack for the wing. The angle of attack, in laymen's terms, is basically how aggressive the wing sits with respect to the wind. If it has more angle, it makes more downforce, but also more drag. If it has less angle...well, the opposite happens. Below is a picture of an airplane wing. You will see that the angle of attack is measured between the wing and the air coming toward it. Don't pay attention to any of the other terms in the diagram for now.
Angle of Attack on an Airplane Wing
My goal was to have an adjustment from close to 0 degrees to something more aggressive. While this was a loose set of criteria, I was concerned the wing would have a negative angle of attack since the stands were not made for my car. This would make LIFT in the rear-- the opposite of what I wanted.
To measure the angle of attack, I first placed a level on the door sill for the driver-side of the car and measured the angle relative to the ground using an app on my iPhone. There are a ton of apps out there that perform this function and if you're a DIY car person you must own one.
Next, I placed my cell phone on the wing and measured the angle of attack at the lowest setting for aggressiveness. I got 2 degrees! Not bad. This meant I had plenty of adjustment if I found I needed more rear downforce at some point. If you'd like to see more about this, just check out the video I referenced below:
Setting Angle of Attack on a Race Car Wing
With the wing fully functional, I decided I'd give it some love and paint it black as well. I purchased four cans of budget paint from Home Depot for a total of $4 and with some 220 grit sandpaper I had laying around, I went to work.
The Wing Sprayed Black
Here's the wing installed:
Front Downforce
Balance is a virtue-- it's one of the valuable qualities for any relationship, the best diet, and of course, the fastest car. With rear downforce only, the car may understeer in high-speed corners, though it may be more stable. The key to a fast car isn't one that understeers, or even one that oversteers, the key to speed is balance.
Stu Chasing Zephyr at New Jersey Motorsports Park
To balance out the rear wing on the Civic, a front splitter is needed. A front splitter increases the pressure on the front of of the car using air pressure differentials. High pressure air goes over the car and low pressure air goes under the car.
Read More About Front Splitters Here
Using Krider Racing's writeup in Speed News, the National Auto Sport Association's magazine, I was able to amass the basic supplies needed for DIY splitter fabrication. However, I incorporated my own twists based on my needs and my resources.
Krider Racing, of NASA SocCal, and Their Acura Integra
One twist was in how I transported my 17/32-inch-thick, 8-foot-long piece of plywood a short distance from Home Depot to my garage in a Chevy Tahoe. This is the LoBuk, Honda Challenge H4 life:
17/32-Inch-Thick Plywood and Garden Edging
Loading an Eight-Foot-Long Piece of Plywood Into a 99 Tahoe
I then borrowed four saw horses, a dual-orbital (DA) sander, a jig saw, and a router from my friend Anthony and got to work. I started by placing the large piece of plywood on the saw horses and taping my front bumper to the plywood.
Most People Don't Tape Bumpers to Wood But I'm a Car Person and I'm Special
Per H4 rules, the splitter cannot extend past the outline of the car when viewed from above, much like the rear wing. So, again, we use plumb bobs to account for this factor. The plumb bob is moved about the front of the bumper and marks are made along the perimeter so you know where to cut.
Using a Plumb Bob to Draw a Splitter Pattern
Additionally, the rear of the splitter cannot extend past where the front wheel wells begin. Luckily, I dealt with this last year when I made an under tray out of corrugated plastic yard signs courtesy of fellow H4 Racer and friend, Ken, Owner of Ken's House Wash. I simply marked where I needed to cut the rear of the splitter based off of the under tray I made for last year.
Undertray Made From Corrugated Plastic
Then, with my friend Alex I began cutting the splitter using the jigsaw Anthony gave me.
Me Cutting Plywood with a Jigsaw
We then used the router to round off the edges of the splitter.
Alex Attaching a Router Bit to Anthony's Router
With the splitter cut and sanded down, we mocked it up underneath of the car to see how it would look.
Splitter Under Civic
Next, we needed to mount the splitter to the car. There are a couple of trick methods for this. For example, Special Projects Motorsports sells the Kiwi Splitter Brackets. These brackets are quick-release and are half-aluminum, half-steel. The steel part mounts to the frame and the aluminum part mounts to the splitter, so if you crash, the frame doesn't bend-- the aluminum brackets do. Additionally, the quick-release is super easy to work with and most racers in Honda Challenge love them.
Kiwi Splitter Mounting Brackets
However, this car is a budget build and we don't have $198.00 to spend on splitter brackets. That money is much better spent on suspension upgrades or reliability upgrades. So, I used some brackets that a friend, and also fellow H4 Racer (see a trend?), Carlos gave to me.
Carlos's Two-Piece Splitter Brackets
Carlos made these brackets for the EF/CRX chassis. The brackets are intended to mount to the frame rails where the tow hooks are originally located. However, the EF and the EG/DC Hondas have their tow hook mounts positioned differently relative to the ground. The EF tow hooks sit higher, and as a result I had to remove the middle section of the splitter brackets circled below:
Where I Had to Modify my Friend's Brackets
The next thing I did was add capture nuts to the brackets. I knew I didn't want to mess around with two wrenches in a cramped space in the engine bay, so I welded some metric nuts from Home Depot that share common Honda diameters and thread pitches.
I always try to add redundancy to the car in this manner so that if a bolt strips, breaks, or gets lost somewhere on the chassis, there is another bolt to replace it.
Capture Nuts Welded to Carlos's Splitter Brackets
I then mocked up these new brackets on the splitter, relative to the chassis, to drill holes.
Mocking up the Splitter Brackets to the Splitter
Next, I began attaching the garden trim to the splitter. There are two trims that need to be attached. The first is a stout, short trim that mounts to the splitter with course screws (#12 X 3/4 wood screws).
It serves as the base for the taller garden trim which I secured to the shorter trim with nuts and bolts. Below you will see the first stage, securing the stout, short trim to the splitter with course screws:
Short Garden Edging Secured to Plywood with Course Screws
Then I took garden edging and drilled holes at equal lengths along the its perimeter and secured it to the garden trim using SAE nuts, metal screws, and washers that you can find in any hardware aisle for about $10. Another option is to use long rivets, but these are harder to find.
The picture below shows me sanding the fake wood grain out of the trim because wood grain only looks good on luxury cars.
Sanding the Fake Wood Grain Out of the Garden Edging
After sanding the garden trim and splitter blade, I cleaned with acetone to remove any dust or dirt which would interfere with paint adhesion.
Prepping Surfaces for Paint
And finally, I laid down a solid base coat of flat black which acts as primer (a trick I learned from an OG) and once that was dry, I laid down two coats of gloss black. Again, I spent $4 on the budget spray paint that Home Depot sells. Regardless of paint quality, it came out pretty good-- serving the old adage that it's all in the prep work.
Painted Splitter
Here are some pictures of the finished car with aero: